Roller Conveyor Products & Components
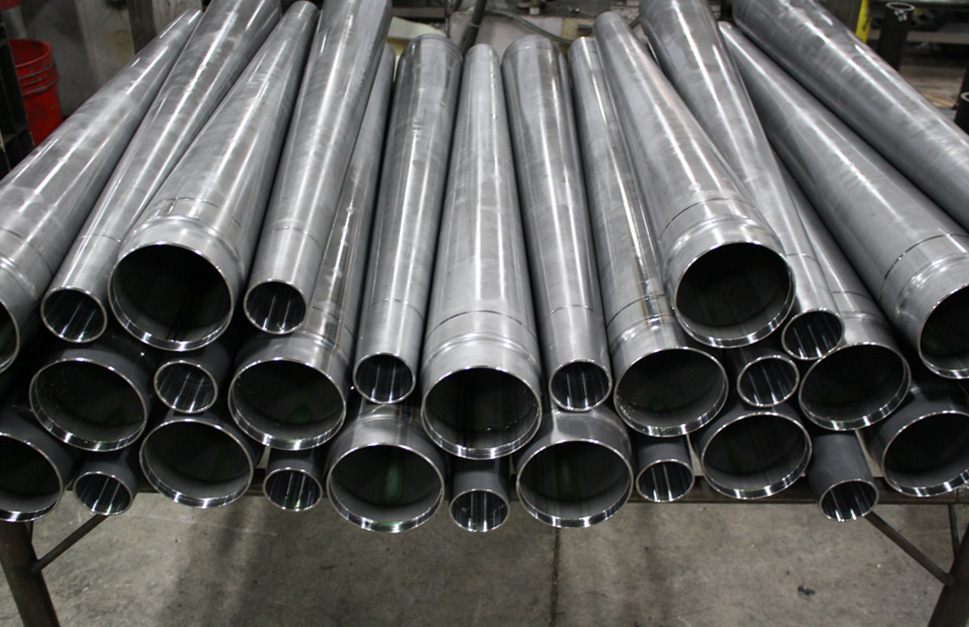
Bryant has long been known as a manufacturer of high quality and innovative conveyor components including Telescoper® takeups, Teletrack heavy and light duty rollers, high precision pulleys, and Airform® tapered rollers and pulleys for both unit and bulk materials.
By pioneering in the fields of tube forming with our Airform® technology, ultra-high precision belt pulley development, and our exclusive TuffCote® urethane coatings, we’ve earned recognition as the leading innovator for quality, custom conveyor parts in the industrial material handling industry.
Staying customer focused, we have learned the key to continued growth is going beyond what our competition does not, cannot, or will not do.
Please select one of our product lines below to learn more.